When a repeat customer approached our precision machine shop with the design for an optical assembly, they had a seriously challenging requirement: for the focus to be adjusted in fine enough increments, they needed a screw with 200 threads per inch (TPI), the equivalent of 0.005” per revolution.
To provide some context, 100 TPI is generally considered a fine pitch for an adjustment screw, and the finest pitch commercially available at the time was 170 TPI. Many “smooth” turned surfaces are machined at a higher feed than .005” per revolution, so they were asking for extremely fine threads.
No stranger to complex machined parts, this customer knew from the start that most precision machine shops would no-quote this particular optical assembly, so they came straight to Wagner Machine, where we’ve developed a reputation for making the impossible possible.
The Challenge: A Complex Optical Assembly
The assembly design consisted of a male and female part: one made from brass and the other from stainless steel. (If both parts had been made from stainless steel, there would have been a risk of them binding up during use.)
Just as the threads were non-standard, the fit between the parts was a non-standard thread fit. Because the diameter was substantially larger than the part length, the fit between the parts required almost zero clearance to limit lateral or angular movement.
The Solution: Wagner Machine’s Precision Machining Process
Wagner Machine’s approach to completing our customer’s complex optical assembly included using custom-ground tools and leveraging our CNC milling capabilities.
Custom-ground tools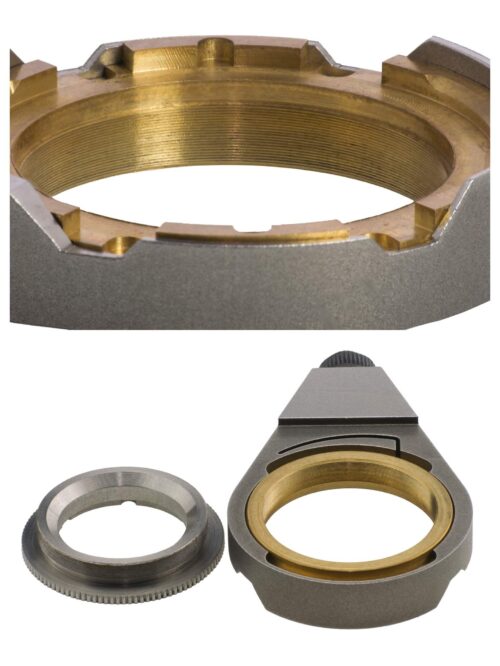
Perfectly sharp threading tools typically don’t hold up well during machining operations, so standard threading tools always have a radius at the tip. This .002” radius on many small threading inserts is great for your average small thread, but it is huge when machining an adjustment screw with 200 TPI; the tool simply isn’t small enough to cut threads that fine because the radius is almost half of the full thread size.
We ended up using custom-ground threading tools. These tools, which came to complete points with no radius on the ends, were the right size to achieve the 200 TPI threads, but we had to control speeds and feeds very carefully to ensure the tips didn’t break during machining on the stainless steel component.
CNC milling
The parts in the assembly were round with critical milled features. Typically, we would turn these parts on a lathe with live tooling, or have separate lathe and mill operations. However, the parts had thin walls and we were afraid that the clamping forces on the lathe might distort them.
Because of the amount of mill work on the parts and our concerns about distortion, we machined each part entirely on a CNC mill. Thread milling gave us better control of the threading process because we could control the surface footage (RPM) of the tool and the feed rate independently, and milling the part complete in one operation ensured we didn’t have clamping forces distorting the part.
The Outcome: A Successful Prototype Machining Project
We manufactured six sets of these complex machined parts for our customer’s optical assembly, successfully completing this challenging prototype machining project.
Initially concerned about tool wear due to the sharp tip on the threading tool while machining stainless steel, we were pleased to find that there was no wear after completing six sets of parts. No offsets were required after initially dialing in the process, and as a result, we’re confident that the process we developed could be used to manufacture these parts in production quantities.
The Impossible Is Possible at Wagner Machine
This project is just one example of our willingness and enthusiasm to create complex machined parts, and we regularly machine small parts that rival this in complexity.
When you need a part you’re certain no shop will quote, give Wagner Machine a chance. Request a quote today!