At Wagner Machine, we’re proud of our precision machine shop’s ISO 9001:2015 certification. The ISO 9001 international standard, first established in 1987 and last updated in 2015, demonstrates our manufacturing process adheres to customer and regulatory requirements.
While the ISO criteria establish minimum standards for all certified shops to meet, our processes and procedures are unique to Wagner Machine. Our specific implementation provides many benefits to our shop and customers. We have created a streamlined manufacturing process and our adherence to ISO 9001:2015 ensures that process is consistent and verifiable for every job we do.
In other words, our customers know that when we say we are going to do something a certain way, we do it that way.
Our Journey to Becoming ISO 9001:2015 Certified
Many of our customers aren’t familiar with ISO 9001:2015 certification or think it equates to more cost and red tape for them. Admittedly, we also wondered if becoming certified was worth the effort. For years, we operated in compliance with ISO standards without having an official certification. But one big opportunity changed our minds.
An existing customer had a high-volume production job that required ISO 9001:2015 certification. We had already completed low-volume prototype batches of these parts with our ISO compliant processes. The realization that a lack of certification was the only thing standing in the way of great production work pushed us to complete the process to become certified. (Fortunately, the company still found a way to work with us before we were certified because no other precision machine shop could match our quality at such a great price. However, extra work was required to ensure that both sides met all regulatory requirements.)
How ISO 9001:2015 Certification Improved Our Precision Machine Shop
The ISO 9001:2015 standard allows us to better identify gaps in our processes and provide a framework for continuous improvement. It also helped us create a strong culture of accountability, allowing us to know exactly who worked on a part and when. In an era of complex supply chains, we can easily trace the origins of materials, the processes and specific equipment used to make parts, the machinists who worked on the jobs, and our in-process and final inspections.
Overall, we can now honestly say that becoming ISO 9001:2015 certified has made us a better AND more efficient shop—in some ways that we didn’t even anticipate.
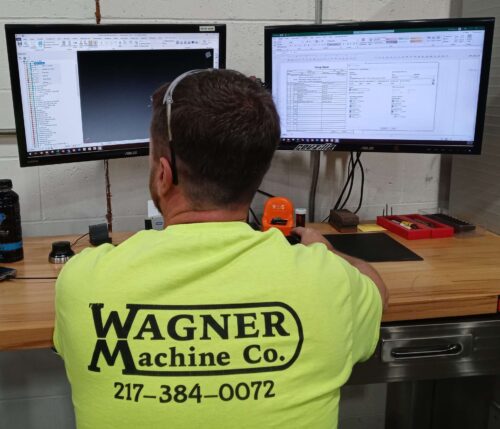
1. Data helps solve the actual problems
When you’re machining parts with tight tolerances and complex features, there’s little room for error. If a problem does arise, our processes help us quickly identify the issue, determine the root cause, and prevent similar instances in the future.
We had a customer who previously didn’t see a benefit to our ISO 9001:2015 certification and came to us when their relatively simple parts failed in the field. Their initial hypothesis was that the material used for the parts was defective because this was a legacy product that had never experienced this type of failure. Our processes allowed us to quickly trace material certs to the specific lot and job. We found that material from the same lot had been used in other batches of parts that were working as intended.
After ruling out the possibility of problematic material, the source of the failure was tracked down to improper operation of a specific piece of equipment by the end user. Complete and traceable documentation helped our customer find the actual cause of the problem and a solution for it.
2. Better customer communication
As an ISO 9001:2015 certified shop, we can not only identify what’s not working but also what’s going well. The 2015 revisions to the ISO 9001 certification require us to verify that we’re making progress toward measurable goals.
For example, we have drastically improved our lead time accuracy. In the past we consistently quoted 4-6 weeks for every project, the same way a pizza place always says it will take 45 minutes for delivery – and our results were equally bad! We didn’t realize how bad until we started tracking.
Continuous improvement driven by our quality management system led to organizational and scheduling process changes. These changes have led to better communication with our customers and improved workflow in the shop. As a result, our on-time deliveries have significantly improved.
3. More data, less guesswork
ISO 9001:2015 certification has made us a more data-centric company. We have always collected plentiful data but never knew quite what to do with it. As a result, we relied too much on intuition and gut feelings to make business decisions.
Today, the world runs on data, and we have adapted accordingly. Thanks to the processes required for ISO 9001:2015 certification, we’ve taken much of the guesswork out of our operations. We can effectively sort through the noise in our data by establishing key performance metrics to measure our business against. These efforts improve our efficiency and allow us to pass those benefits on to our customers.
We’ve always prided ourselves on our top-notch machining capabilities. But our decision to invest the time and effort to gain ISO 9001:2015 certification has upped our game. We diagnose problems faster, offer more accurate information to our customers, and constantly improve our business by establishing a strong culture of transparency and accountability.
Sound good to you? Request a quote to work with us!